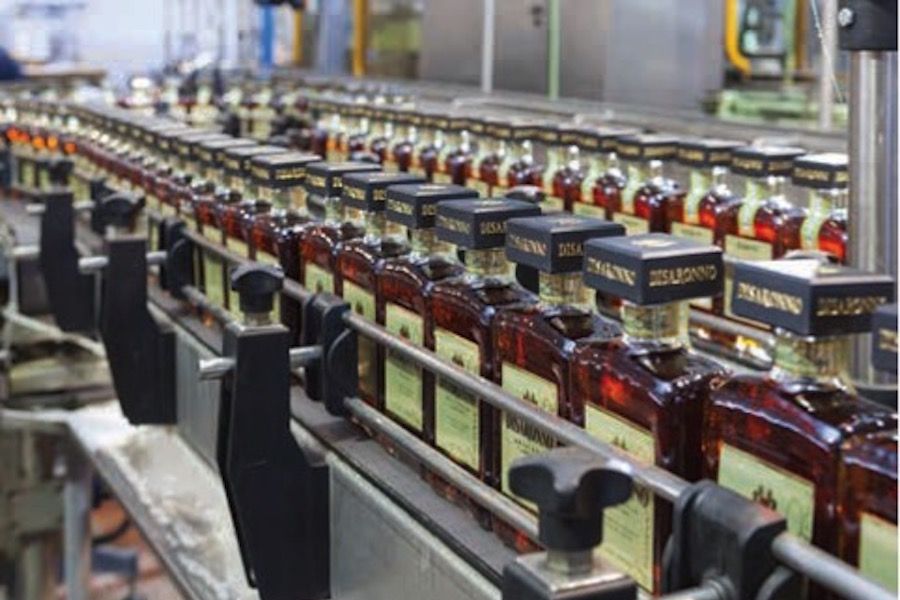
Illva Saronno, sapore di innovazione nel dialogo tra macchine e software
La storia di Illva Saronno inizia con una leggenda che ha per protagonisti un pittore allievo di Leonardo da Vinci (Bernardino Luini), una locandiera di Saronno, così bella da posare come modella per la Madonna dei Miracoli del locale Santuario, e un liquore ambrato, la cui ricetta risale addirittura al 1525 e venne tenuta segreta e tramandata all’interno della famiglia Reina per secoli.
Fu solo nel 1947, infatti, che l’azienda venne fondata e l’antica ricetta tramutata nel liquore divenuto iconico: il Disaronno. Oggi, l’Illva Saronno è un’impresa con circa 150 dipendenti e un fatturato di 150 milioni di euro ed è rimasta a conduzione familiare, controllata dai discendenti del fondatore, Domenico Reina, attraverso l’Illva Saronno Holding, presieduta e amministrata da Augusto Reina.
Alla holding fanno capo diverse società operative, attive in più settori di business. Il principale è quello degli Spirits, gestito dalla società Illva Saronno, che produce e commercializza brand come Disaronno, il prodotto principale, Tia Maria, Rabarbaro Zucca, Artic Vodka, Aurum e altri.
La produzione è tutta concentrata a Saronno, dove si trovano gli stabilimenti produttivi. Il business Wine, invece, è gestito dalla società Duca di Salaparuta, che produce vini a marchio Corvo, Duca di Salaparuta e Marsala Florio.
La produzione è in Sicilia, mentre l’headquarter commerciale e i servizi generali sono a Saronno, dove ha sede la società Real Aromi, che produce aromi industriali; mentre le società Prodotti Stella e Montebianco, operative nel mondo dei semilavorati per gelaterie, pasticcerie e bakery per la grande industria, hanno gli stabilimenti a Chignolo, in provincia di Pavia, e ad Altavilla Vicentina.
Oltre alle società operative in Italia, la holding ha filiali commerciali anche all’estero, soprattutto dell’Illva Saronno: in Svizzera, Olanda e negli Stati Uniti. Il business dell’impresa è fortemente concentrato verso l’estero: l’export incide per circa l’80% del fatturato.
Inoltre, la holding ha partecipazioni dirette o collaborazioni estere in mercati strategici in Asia: ha rilevato un terzo della società cinese Changyu, leader asiatico nella produzione di vini, e ha costituito una joint venture paritaria con Umesh Modi Group per la distribuzione dei suoi prodotti in India.
“Sono partnership molto importanti, strategiche per noi e per la nostra evoluzione, in due mercati con un focus importantissimo come margine di crescita e di distribuzione dei prodotti”, spiega a Sistemi&Impresa Antonio Pisano, Direttore dei Sistemi Informativi di Illva Saronno Holding.
L’innovazione dello stabilimento
Lo stabilimento di produzione è stato recentemente rinnovato, sia nell’ottica di potenziare l’attività attuale sia in quella di lanciare nuovi prodotti. L’obiettivo è quello di perseguire una continua evoluzione della capacità produttiva e della qualità dei prodotti. A questo scopo è stato avviato un processo di rinnovamento delle macchine.
“Attualmente è in corso un’attività di aggiornamento del sito produttivo: si sta lavorando non solo dal punto di vista delle macchine, ma c’è anche un’attività molto forte di informatizzazione dello stabilimento stesso, nell’ottica di un progetto 4.0”, racconta Giuseppe Marino, Direttore di Stabilimento Illva. La spinta all’innovazione arriva dalla proprietà.
“C’è un supporto molto forte da parte della proprietà, che sta spingendo in questa direzione. L’Industria 4.0 è un elemento cardine del progetto che punta a farci ottenere un miglior controllo delle attività, delle macchine e delle performance delle stesse e una più ampia gamma di informazioni disponibile per tutti”. L’obiettivo è che “tutte le persone interessate abbiano tutte le informazioni necessarie sempre a disposizione, cosa che non accade con i criteri canonici di informatizzazione”.
A questo scopo, l’azienda ha deciso di implementare il Manufacturing Execution System (MES), un’interfaccia tra le varie divisioni che consente a tutti di avere sempre visibile l’andamento della produzione. “Nell’arco del 2018 abbiamo inserito due linee nuove, automatizzate e integrate con i nostri sistemi gestionali centrali”, racconta Pisano.
Nello stabilimento di Saronno ci sono sei linee di produzione: le due oggetto del progetto MES di Industria 4.0 sono le principali, quelle dedicate alla produzione del Disaronno. “Le linee sono state completamente rifatte, puntando a implementare in azienda lo stato dell’arte della tecnologia, sia dal punto di vista meccanico sia di supervisione e controllo tramite software”.
Le linee, che sono andate in funzione alla fine del 2018, sono gemelle: ogni macchina che fa parte di questa linea è dotata della propria ‘intelligenza’: un controllore logico programmabile (PLC) che ne governa l’operatività.
“Durante questo progetto di reingegnerizzazione delle linee, uno dei punti importanti che ci siamo prefissati all’inizio era l’integrazione dei sistemi di fabbrica e dei PLC di campo con i sistemi centrali, tramite una soluzione di tipo MES”, aggiunge il Direttore dei Sistemi Informativi.
L’implementazione del sistema MES
Per realizzare il sistema, messo a punto nei primi mesi del 2019, l’azienda si è appoggiata a un partner, Zenith Automazione, per avere supporto dal punto di vista tecnologico nell’implementazione di una soluzione di Wonderware, uno dei maggiori player internazionali in questo ambito.
“La soluzione MES di Wonderware si pone come ponte e punto di congiunzione tra i nostri sistemi centrali e gestionali, l’ERP tradizionale, dove svolgiamo le attività di pianificazione della produzione, e il campo, i PLC della linea”. Sostanzialmente la soluzione MES raccoglie gli ordini di imbottigliamento generati dal sistema gestionale ERP.
“Sul MES operiamo un’attività di programmazione della produzione giornaliera o settimanale al massimo, mettendo in sequenza gli ordini di imbottigliamento. Lavoriamo cercando di ottimizzare e ridurre il numero di cambio dei formati e i tempi di attrezzaggio”, sottolinea Pisano.
Una volta definita la sequenza degli ordini di imbottigliamento, il MES li trasmette al campo, sulle linee e ai PLC delle varie macchine che compongono la linea di produzione. Inoltre, invia anche il setup necessario per produrre un determinato prodotto: la tipologia di bottiglia, di tappo, di etichetta, di pallet e di cartone che deve essere utilizzato.
“Ogni macchina si predispone in automatico per il proprio setup. Questo l’abbiamo voluto per ridurre i tempi di attrezzaggio e gli errori manuali nella configurazione delle macchine”. La comunicazione non va solo dal sistema centrale verso il campo, c’è anche un ritorno dei dati dal campo al sistema centrale. “Ogni macchina risponde al MES fornendo il dettaglio delle quantità prodotte, dei consumi di materiale di confezionamento per ogni stazione, i tempi effettivi di produzione, i guasti macchina, gli allarmi macchina ed eventuali causali di fermo macchina”.
Questa mole di informazioni viene registrata su un database dedicato e utilizzata per analizzare i rendimenti effettivi delle macchine e della linea nel suo complesso, evidenziare eventuali punti di criticità, rotture frequenti e altro ancora. “Il sistema MES produce informazioni a 360 gradi. Per esempio, in magazzino, sappiamo che materie prime stiamo finendo e dove mettere il prodotto finito”, evidenzia Marino.
Il nuovo sistema di management permette una tracciabilità del materiale interna ed esterna completa. “Così riduciamo gli eccessi in stock e produciamo di più su commessa invece che attraverso il magazzino”.
Le nuove linee ‘su misura’ del Disaronno
Le due nuove linee implementate nello stabilimento di Saronno sono dotate di macchine innovative, automatizzate, integrate con il sistema centrale, ma soprattutto realizzate su misura per la produzione delle bottiglie di Disaronno, che sono di forma rettangolare e con il tappo quadrato. “Sono macchine ‘cucite su misura’ per il particolare prodotto specifico Disaronno che, dal punto di vista dell’imbottigliamento, presenta problematiche che non sono comuni alle normali bottiglie tonde”.
La scelta, non automatica, di adattare le macchine alla forma della bottiglia e non viceversa deriva dalla storia del prodotto e da specifiche ricerche di mercato. “Si tratta di una forma storica, diventata iconica, a cui i consumatori sono affezionati. Perciò l’azienda ha deciso di conservarla, anche se ha bisogno di macchinari su misura per maneggiarla”.
A essere tailor-made non sono solo le macchine che riguardano le bottiglie, ma anche i tappi, i manipolatori, le rastrelliere, ecc. Le nuove macchine, inoltre, permettono una produzione con maggiore flessibilità, un setup della linea più veloce e anche una migliore manutenzione.
“In più, permettono di ridurre il numero delle persone necessarie a bordo linea, che possono così essere impiegate altrove”, rivela Marino. Tuttavia, rimangono ‘umane’ alcune funzioni, come quella del controllo di qualità visivo, che viene fatto dal personale, in aggiunta al sistema di controllo delle macchine.
Gli obiettivi raggiunti e i progetti per il futuro
L’innovazione dello stabilimento ha come obiettivi principali il miglioramento della produttività delle linee in termini di bottiglie- ora (+50%) la riduzione dei tempi di attrezzaggio e setup (–70%), una maggiore flessibilità nella gestione dei cambi formato per permettere una pianificazione più efficace e una riduzione dei fermi dovuti ai cambi.
“Con la vecchia linea, i tempi di attrezzaggio richiedevano circa un turno o un turno e mezzo di lavoro, quindi dalle 8 alle 12 ore. Un obiettivo importante che abbiamo raggiunto è di farli passare a mezz’ora o un’ora”. Tra gli obiettivi annoverati da Illva c’è anche la riduzione del 20% dello stock del prodotto finito.
“Prima alcuni formati venivano prodotti più saltuariamente e stoccati. Oggi ci possiamo permettere di produrre formati differenti non solo più volte in un mese, ma addirittura nell’arco di una settimana”. Infine, un altro obiettivo era di andare verso le produzioni su commessa.
“Questi sistemi di controllo ci permettono di produrre esattamente il numero di bottiglie che il mercato ci chiede, senza avere un over-stock a fine produzione. Le vecchie linee, invece, non essendo automatizzate, non permettevano questo controllo alla bottiglia, quindi si produceva facilmente mezzo pallet in più, con tutte le problematiche di gestione del magazzino”.
L’azienda sta lavorando anche per migliorare e potenziare le altre quattro linee presenti nello stabilimento di Saronno, che attualmente sono specifiche per tipologia di prodotto. “Le altre quattro linee sono automatizzate, ma più ‘vecchie’ e meno performanti. Perciò è probabile che si vada a operare con un’ulteriore nuova linea o con un progetto di ristrutturazione delle linee esistenti”.
Nel mese di settembre 2019 intanto è partito un progetto analogo con una terza linea, gemella delle altre due, in Sicilia per l’imbottigliamento dei vini. “E per il 2020 stiamo già ragionando su eventuali inserimenti di una soluzione simile sulle altre linee che sono qui a Saronno e sono rimaste su un modello tradizionale”.
Per quanto riguarda nello specifico la sorte dello stabilimento di Saronno, il nuovo Direttore di Stabilimento ha le idee chiare. “L’obiettivo è di rendere le linee più flessibili e accorpare la produzione, aumentando lo spazio a disposizione e la produttività”.
industria 4.0, nuove tecnologie produzione, Manufacturing Execution System, Illva Saronno Holding, Antonio Pisano