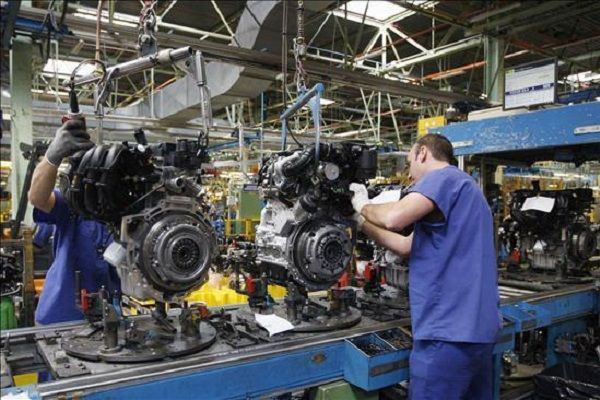
Il coronavirus ridisegna le filiere: la produzione localizzata di Brovedani
Prima lo stop produttivo in Cina, poi la quarantena italiana. Il Covid-19 per il mondo dell’impresa rappresenta allo stesso tempo un ostacolo e una sfida. Lo choc economico cinese ha fatto sì che per alcuni settori, in particolare quello della Meccanica, le forniture che non arrivavano da Pechino venissero dirottate su aziende italiane. Tuttavia questa opportunità rischia di essere ininfluente se l’industria europea dovesse fermarsi.
“Dovremo vedere cosa succede nelle prossime settimane a tutta la filiera a partire dal mondo tedesco. A oggi non abbiamo avuto modifiche di ordinativi. Però ci aspettiamo che i consumi abbiano un contraccolpo in tutto il mondo. Per il settore manifatturiero lo Smart working non è una soluzione. Il rischio è che si fermi la produzione”, spiega Sergio Barel, Direttore Generale e Amministratore Delegato di Brovedani, gruppo da 120 milioni di ricavi, leader nel settore della componentistica auto e delle automazioni in ambito industriale.
L’azienda ha avuto una commessa incrementale per un prodotto su cui era in code sharing con un fornitore cinese e ora si trova a dover far fronte alle restrizioni e ai limiti stabiliti dal Governo a seguito dell’aumento dei contagi da coronavirus in Italia. “Questa crisi può incentivare una serie di ragionamenti su una maggiore regionalizzazione delle filiere, almeno nel campo Automotive. In Europa questo tipo di riflessione tardava, ma ora questa tragedia la riporta al centro”, osserva Barel.
Ma non sarà la fine della globalizzazione. I player continueranno a essere globali, ma localizzati nei mercati. Quindi si produrrà nelle aree di vendita. Secondo l’AD di Brovedani per i lavoratori questo trend può avere effetti positivi. L’internalizzazione rimarrà la chiave, ma ci saranno meno delocalizzazioni. “Ricostruire intere filiere sarà una sfida. Oggi, per esempio, l’Europa si accorge improvvisamente di non essere capace di produrre una mascherina. Saremo costretti a rivalutare una serie di competenze e capacità che avevamo messo in basso nella lista dei valori. Questo sarà uno dei pochi lati positivi di questa tragedia”.
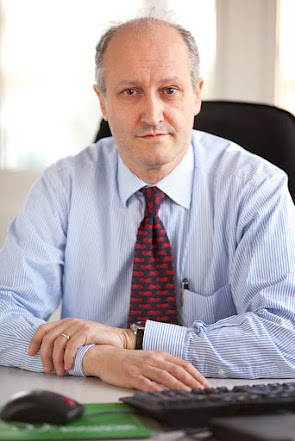
Impostare l’organizzazione flessibile
Per far fronte ai cambiamenti sul mercato, la domanda e l’offerta dovranno essere sempre più flessibili. In un business capital intensive come quello di Brovedani questo significa garantire la produzione anche nel terzo turno notturno e nei weekend per riuscire ad affrontare con velocità i cambi di ritmo. Regole che in alcuni Paesi all’estero sono standard, ma non in Italia.
“In Italia abbiamo accordi sindacali in essere che ci consentono di attivare in forma veloce aumenti di orario con diverse modalità. Ovviamente è necessario avere persone formate sui mezzi produttivi e avere un processo a monte che garantisca di avere dipendenti in grado di cambiare lavoro in tempi brevi”, racconta il manager.
Brovedani conta sette società e 10 unità produttive, dislocate in Italia, Slovacchia e Messico. La direzione e il cuore dell’engineering sono a San Vito al Tagliamento, in provincia di Pordenone. Il processo di riorganizzazione aziendale negli anni è stato orientato verso un sempre maggiore decentramento operativo, mantenendo tuttavia un forte coordinamento dal punto di vista delle linee guida e del controllo della gestione. Questa struttura matriciale è indispensabile per unire la reattività al mercato, che non può essere che su base locale, alle linee di sviluppo che devono essere più centralizzate.
“Le decisioni operative vanno prese vicino al cliente. Sarebbe impensabile decidere dall’Italia cosa fare in Slovacchia o in Messico. Questo significa decentrare competenze tecniche e gestionali e creare team all’estero, che lavorino con quelli italiani ma siano anche sufficientemente autonomi”.
Investire su formazione e innovazione
La formazione rappresenta un elemento fondamentale per l’azienda. Molti dipendenti delle sedi all’estero hanno fatto tirocini di settimane o mesi nella sede centrale. Inoltre tutte le società che compongono il gruppo hanno relazioni continue con università e sedi formative locali da cui attingere e fruire conoscenze.
Nel 2006 il gruppo Brovedani è stato uno dei soci fondatori del Centro di Innovazione, ricerca e formazione Keymec di San Vito al Tagliamento, nato per accompagnare le aziende del settore della meccanica in un processo di crescita e sviluppo tecnologico, formando ricercatori e tecnici capaci di gestire le fasi di ingegnerizzazione nei settori della ricerca tecnologica avanzata e manager esperti in processi di qualità e di organizzazione complessi con le tecniche Lean, in quegli anni non ancora sviluppate come oggi.
Oltre agli investimenti in formazione, ciò che ha consentito all’azienda di mantenere la competitività degli impianti, soprattutto a cavallo della crisi del 2009, è stata proprio la filosofia Lean. Negli ultimi 10 anni questo approccio ‘snello’, adottato dalla Toyota già negli Anni 90, ha coinvolto soprattutto il Manufacturing. Già nel 2006, il gruppo industriale Delphi, cliente di Brovedani, propose all’azienda di mandare a San Vito al Tagliamento un esperto di lean per ridurre il tempo di passaggio da una produzione all’altra. La fabbrica venne completamente rivoluzionata (non mancarono dubbi e resistenze da parte dei dipendenti, che furono in parte superate introducendo il cambiamento a piccoli passi, attraverso progetti pilota).
Nel 2011 la realtà Keymec è confluita in Lean Experience Factory 4.0, un centro di formazione esperienziale con sede a San Vito al Tagliamento, nato nel 2011 dalla joint venture tra McKinsey & Company e Unindustria Pordenone, Confindustria Udine, Polo Tecnologico di Pordenone, Consorzio Ponte Rosso, CCIAA di Pordenone. Oggi Lean Experience Factory è un Digital Innovation Hub a livello nazionale e internazionale.
Approccio di team e contatti con i clienti
Ora la sfida è applicare queste tecniche a tutti i processi indiretti. Questo passo va collegato con la digitalizzazione di tutte queste fasi. “La digitalizzazione è un’occasione per efficientare i processi, se sono già lean, altrimenti rischiamo di digitalizzare le inefficienze. La grande montagna da affrontare è il cambiamento delle persone. Siamo partiti dagli operai. Cambiare il metodo di lavoro dei tecnici è ancora più difficile”, ricorda Barel. Oggi serve un approccio molto più di team rispetto al passato e il contatto con il cliente deve essere sempre più frequente.
Sul fronte della digitalizzazione in ambito industriale, uno dei primi passi per l’azienda è stato lo sviluppo di un sistema proprietario di controllo visivo e dimensionale dei pezzi prodotti, sviluppato insieme con partner locali. Questa architettura hardware-software si interfaccia con l’automazione di impianto e permette di monitorare il 100% della produzione.
Le singole società erano andate avanti nello sviluppo della digitalizzazione dei vari processi usando team locali, in parallelo. Questo ha consentito di accelerare le esperienze a scapito di una certa sovrapposizione. “Ora abbiamo formato un team internazionale che sta selezionando le best practice delle varie società per poterle poi applicarle ovunque e diventare lo standard aziendale”, dice Barel. L’Italia, per esempio, è molto più avanti sulla connessione delle macchine, la Slovacchia sul fronte della gestione della manutenzione, il Messico sulla preparazione di sistemi semplificati di dashboard.
Nel frattempo, con l’acquisizione della FreTor e l’entrata nel mercato delle automazioni e della fornitura di sistemi produttivi, l’azienda è in grado di mettere insieme le esperienze digital di chi usa i sistemi in produzione e di chi li progetta e costruisce: una competenza unica nel suo genere.
Nei piani futuri dell’azienda c’è l’integrazione di funzionalità di Intelligenza Artificiale (AI) per potenziare lo sfruttamento dei dati raccolti per analisi predittive a fini di manutenzione, controllo qualità e correzione automatica dei processi. “Vogliamo far diventare una grande opportunità l’AI. Noi siamo contemporaneamente luogo di applicazione e anche fornitori di sistemi digitalizzati per l’Automotive. Poter mettere a fattore comune queste due esperienze ci dà l’opportunità di sviluppare nuovi mercati e nuovi settori e di cavalcare questa grande trasformazione”, conclude Barel.
lean production, Intelligenza artificiale, innovazione formazione, Brovedani